Thermoplastic Polyurethane (TPU): A Comprehensive Material Guide
- alisonpitt
- Jun 3, 2024
- 4 min read
Updated: Jul 5, 2024
Thermoplastic Polyurethane (TPU) is a versatile and resilient thermoplastic elastomer known for its exceptional elasticity, transparency, and resistance to oil, grease, and abrasion. Its unique combination of properties makes TPU a popular choice in a variety of industries, from automotive to consumer electronics. This guide will explore the properties, benefits, applications, and processing methods of TPU, providing a thorough understanding of its value in modern manufacturing.
What is Thermoplastic Polyurethane (TPU)?
Thermoplastic Polyurethane (TPU) is a class of polyurethane plastics that combines the characteristics of both rubber and plastic. It is formed through the reaction of diisocyanatos with polyols, creating a polymer that can be processed like a thermoplastic but exhibits the properties of an elastomer. TPU is available in different hardness levels, ranging from soft and flexible to hard and rigid, allowing for a wide range of applications.
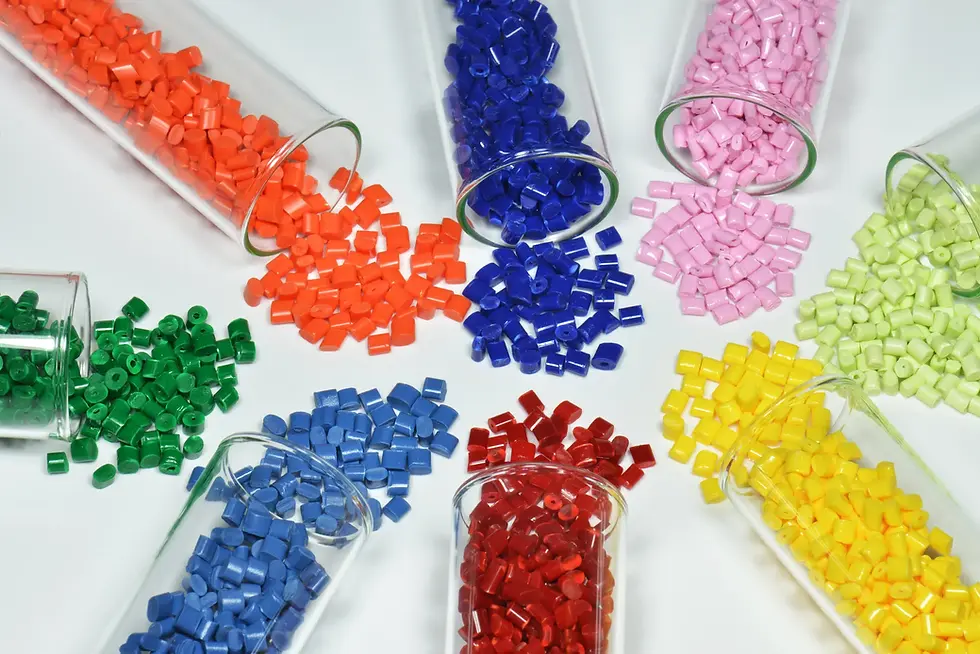
Key Properties of TPU
High Elasticity: TPU exhibits excellent flexibility and elasticity, allowing it to stretch and return to its original shape without permanent deformation.
Transparency: TPU can be produced in a transparent form, making it suitable for applications requiring clarity.
Abrasion Resistance: TPU offers outstanding resistance to wear and tear, making it ideal for high-wear applications.
Chemical Resistance: TPU is resistant to oils, greases, and many solvents, enhancing its use in harsh environments.
Temperature Stability: TPU maintains its properties over a wide temperature range, performing well in both hot and cold conditions.
Tear Resistance: TPU has high tear strength, ensuring durability and longevity in demanding applications.
Ease of Processing: TPU can be easily processed using standard thermoplastic methods, such as injection moulding and extrusion.
Recyclability: TPU is recyclable, contributing to environmental sustainability.
Applications of TPU
Due to its impressive properties, TPU is used in a wide array of applications, including:
Automotive: Protective films, seals, gaskets, and interior components due to its durability and flexibility.
Footwear: Soles, midsoles, and uppers because of its elasticity, abrasion resistance, and comfort.
Consumer Electronics: Phone cases, wearable device straps, and protective covers benefiting from its flexibility and durability.
Medical Devices: Tubing, catheters, and medical instrument components due to its biocompatibility and sterilisation capability.
Sporting Goods: Protective gear, inflatable products, and performance apparel taking advantage of its flexibility and resilience.
Industrial Applications: Hoses, conveyor belts, and seals where abrasion resistance and chemical stability are crucial.
Textiles: Coatings and laminates for fabrics, providing water resistance and flexibility.
Processing Methods for TPU
TPU can be processed using various methods, each suitable for different types of products:
Injection Moulding: Commonly used for producing complex shapes and parts with high precision, such as automotive components and consumer goods.
Extrusion: Used to create profiles, sheets, and films by forcing molten TPU through a shaped die.
Blow Moulding: Ideal for making hollow objects like bottles and containers by expanding the plastic into a mould using air pressure.
Compression Moulding: Involves shaping TPU under heat and pressure, suitable for producing large, thick parts.
Thermoforming: Involves heating TPU sheets and forming them over a mould to produce items like trays and covers.
3D Printing: TPU is increasingly used in 3D printing for prototyping and small-scale production due to its flexibility and ease of use.
Advantages of Using TPU
Versatility: Combines the properties of rubber and plastic, suitable for a wide range of applications.
Durability: Offers excellent resistance to wear, impact, and chemicals, ensuring long-lasting performance.
Elasticity and Comfort: Provides superior flexibility and a soft touch, making it ideal for consumer products and medical devices.
Transparency: Can be used in applications requiring clear or coloured finishes.
Temperature and Chemical Resistance: Performs well in diverse environmental conditions and is resistant to many chemicals.
Ease of Processing: Can be moulded and shaped using standard thermoplastic equipment, reducing production costs.
Recyclability: Contributes to sustainability efforts by being recyclable.
Challenges and Considerations
While TPU offers many advantages, there are some challenges to consider:
Cost: TPU can be more expensive than some other thermoplastics, which may impact its suitability for cost-sensitive applications.
Processing Complexity: Requires precise control during processing to achieve desired properties and avoid issues such as moisture sensitivity.
Performance Limits: While versatile, TPU may not match the high-performance characteristics of specialised materials in extreme conditions.
Environmental Impact: Like many plastics, TPU can contribute to environmental pollution if not properly managed and recycled.
Conclusion
Thermoplastic Polyurethane (TPU) is a highly versatile and resilient material, valued for its flexibility, durability, and ease of processing. Its extensive use in automotive, footwear, consumer electronics, medical devices, sporting goods, industrial applications, and textiles underscores its importance in modern manufacturing. By understanding the properties, benefits, and processing methods of TPU, you can leverage its advantages in your applications, ensuring efficiency and performance.
Whether you’re designing durable automotive parts, creating flexible and comfortable footwear, or developing robust consumer electronics, TPU offers the elasticity, durability, and versatility needed to meet your project requirements.
If you're considering plastic injection moulding for your components, schedule a free consultation with us today to explore how we can help bring your projects to life with precision and quality.
Comments