The Injection Moulding Process
- alisonpitt
- May 9, 2024
- 6 min read
Updated: Jun 10, 2024
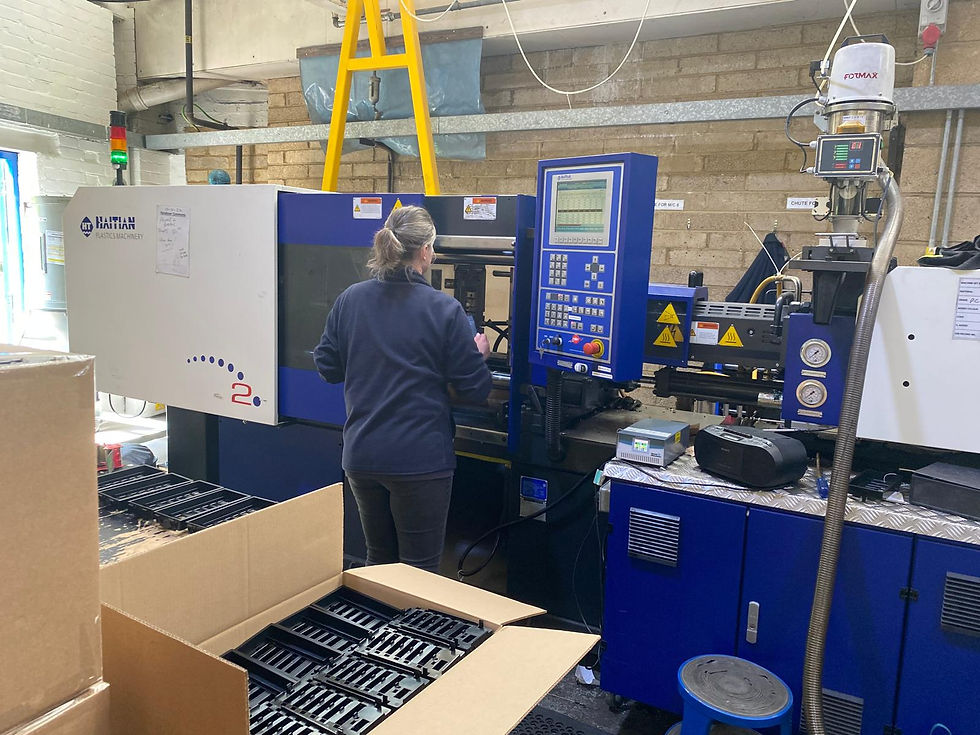
Injection moulding is gaining increasing traction across industries like construction, engineering, and component parts manufacturing due to its versatility, high-quality finishing, and straightforward methodology. This technique accommodates a wide range of materials for producing precision parts, including metals (referred to as die-casting), glass, elastomers, and various plastics like thermoplastics and polymers.
While not a recent innovation, the inception of the injection moulding process dates back to 1872 when American inventor John Wesley Hyatt, along with his brother Isaac, patented the first-ever moulding machine. This early design utilised a large hypodermic needle to extrude melted plastic through a heated cylinder into a predetermined mould shape. Initially, products such as buttons, and hair combs were manufactured using this method. However, the onset of the Second World War fuelled an unprecedented need for cost-effective, mass-produced goods.
What does the injection moulding process entail?
The injection moulding process involves creating plastic products by introducing plastic granules, heating them, cooling them, and shaping them into the desired size and shape. This method enables the rapid production of a multitude of plastic products with high precision. Many of the plastics commonly used in daily life are manufactured using injection moulding.
The selected material undergoes heating before being injected into a specially designed mould, resulting in a component that precisely matches the desired shape, colour, and size for various applications, including machinery, moving parts, and other types of equipment.
Typically crafted from robust tool metals like steel or aluminium, moulds are engineered with precision to endure the rigors of heavy-duty usage and meticulously customised to suit their specific purposes.
Injection moulded parts find applications across a vast range of sizes, from minuscule machine widgets to entire car body panels. Additionally, common uses for injection moulding encompass packaging, automotive components, storage containers, toys, plumbing fixtures, and medical devices.
Injection Moulded Products
The plastic injection moulding process is widely employed across various fields, producing an array of products. Everyday household items such as plastic cups, bowls, plates, and spoons are commonly manufactured through injection moulding. Additionally, products like keyboards, mice, monitor casings, printers, and more are also created using this method.
Toys rank among the foremost and widely sought-after plastic products available in markets. Their design and production are facilitated by the pliability of plastic, allowing for easy twisting and bending.
In the medical field, plastic injection moulding produces essential equipment like syringes, gloves, IV tubes, plastic lenses, protective gear, and various medical tools vital for hospitals and healthcare facilities.
Plastics play a pivotal role in the packaging industry, where they are used to package foods such as salads, meats, and chips, as well as cosmetic items and makeup boxes.
Automotive components benefit from plastics injection moulding, with products like bumpers, dashboards, wipers, and more being widely utilised in vehicles.
Common everyday items such as CDs, DVDs, vending machines, battery casings, and electrical switches rely on moulded plastics for their production, owing to the efficiency and high-volume capabilities of the injection moulding process.
Products made by injection moulding:
The plastic injection moulding process is renowned for its speed and capacity to produce large quantities of identical objects with exceptional precision. The resulting plastic products are lightweight, user-friendly, and contribute to simplifying daily life. Let's explore a few commonly used plastic products manufactured through injection moulding.
Plastic bottles
Disposable cutlery (forks, knives, spoons)
Phone cases
Automotive interior parts (such as dashboard components)
Toothbrushes
Power tool housings
Packaging containers (for food, cosmetics, etc.)
Medical syringes
Computer keyboard keys
Children's toys
The Process of Plastics Injection Moulding
The plastics injection moulding process offers numerous advantages over moulding with other materials like metal or glass. One of its primary benefits is the versatility of plastic, which can be moulded into virtually any colour, shape, or size. Plastic is also durable, hygienic, and readily available. Additionally, many types of plastics, such as thermoplastics, are recyclable, making them an excellent choice for sustainable projects. Below is an overview of the injection moulding process:
Step-by-Step Guide to the Injection Moulding Process
1. The plastic injection moulding process commences with the introduction of raw plastic material, typically in the form of granules or small pellets. These are then fed into a hopper where they are subjected to high heat, causing them to melt. Once the plastic reaches a soft, malleable state, it is injected under pressure into a mould, which can consist of a single cavity or multiple cavities, to form the desired shape or shapes. Subsequently, the plastic parts undergo a cooling period to facilitate hardening and solidification. Once cooled, the injection mould is opened, and the newly formed plastic component is released using moving rods, plates, or an air blast, rendering it ready for its intended application.
2. The mould comprises two distinct components: the injection mould, responsible for shaping the plastic material as it enters the machine, and the ejector mould, which expels the solidified product from the machine, facilitating its progression along the production cycle. It is imperative to handle the moulds with utmost care to extend their longevity. Maintaining ideal humidity and temperature levels is crucial to ensure optimal performance and prevent any potential warping issues.
3. This method is both quick and efficient, allowing for the rapid production of numerous plastic components with consistent shape and size in comparatively shorter durations. Despite its speed, it maintains remarkable precision and delivers a superior quality finish. However, like any manufacturing process, plastics injection moulding is not without its challenges, yet most of these can be resolved with the appropriate technical expertise.
4. Typical issues encountered encompass blistering, burn marks, colour streaking, crazing, and twisting, all of which can compromise the quality and appearance of the plastic components. Therefore, it is imperative to conduct regular maintenance and prompt repairs on injection moulding machines as soon as any issues arise. Additionally, close scrutiny of the plastic parts during production is essential to pre-empt any disruptions in the production cycle.
5. The versatility of the plastics injection moulding process allows for the utilization of various methods to achieve diverse finishes. For instance, a two-shot or multi-shot mould integrates two or more distinct materials into a single finished plastic part. This approach is optimal for achieving softer finishes, such as those required for drawer knobs, or when a part necessitates multiple colours or different yet complementary characteristics.
In an alternative approach, a pre-moulded form can be inserted into a larger mould, with molten plastic poured around it to create the subsequent stage in a more intricate production cycle. This method, known as insert moulding, proves beneficial for crafting plastic parts that incorporate protruding metal bars or screws, as well as for attaching plastic films to plastic food containers.
Pros and Cons of Plastics Injection Moulding
Deciding whether to employ plastic injection moulding in a manufacturing process hinges on project-specific requirements. This method boasts several advantages and drawbacks. Plastic, as a material, offers numerous benefits—it's durable, flexible, and easily shaped to desired forms. Many thermoplastics are recyclable, and plastic products often exhibit longevity, even if not fully recyclable. Its hygienic properties make it ideal for food, beverage, and medical packaging. Plastic can be coloured in myriad shades, used at various thicknesses, and withstand harsh conditions, including temperature extremes, exposure to water, air erosion, and contact with chemicals.
The plastic injection moulding process is quick, with low labour costs and high output capacity. It accommodates the creation of intricate, small parts and allows for the inclusion of inserts like metal screws. Scrap plastic can be recycled, reducing waste. However, drawbacks include significant initial setup costs, as injection moulding machines require substantial investment for installation, setup, and maintenance. Design limitations may arise, contingent upon mould creation capabilities. Smaller production runs may prove less cost-effective due to ongoing expenses and labour. Adequate space, ventilation, and training are necessary for safe machine operation and injury prevention.
Additionally, designing custom moulds for precise component production adds time and expense to projects. Nevertheless, these drawbacks can be anticipated and effectively addressed during the early planning phases.
What products can be manufactured using the injection moulding process?
The injection moulding process is incredibly versatile, enabling the production of a wide range of products across various industries. Common examples include plastic parts for automobiles, consumer electronics, medical devices, packaging materials, household appliances, toys, and many more. From intricate components to simple everyday items, injection moulding offers the flexibility to create diverse products efficiently and cost-effectively.
How does a plastic injection moulding machine operate?
The plastic injection machine consists of three main components: the feed hopper, heated barrel, and screw. Plastic granules are fed into the heated barrel through the hopper. Inside the barrel, the granules are heated using both the heated barrel and the friction generated by the reciprocating screw. Once the plastic is sufficiently heated, it is injected into the mould cavity, where it cools and takes on the desired shape and size. This outlines the basic operation of the injection moulding process within the machine.
We hope this comprehensive exploration of the injection moulding process has provided valuable insights into its versatility, applications, and advantages. If you're considering plastic injection moulding for your component parts or product manufacturing needs, we encourage you to reach out to us. With our expertise and dedication to quality, we're here to guide you through the process and help bring your ideas to life.
To arrange your consultation, call us at 01453 833 388 or email us at tradesales@pnplastics.co.uk
Comentarios