Low-Density Polyethylene (LDPE): A Comprehensive Material Guide
- alisonpitt
- Jun 3, 2024
- 3 min read
Updated: Jul 5, 2024
Low-Density Polyethylene, commonly referred to as LDPE, is a versatile and widely used thermoplastic polymer. Renowned for its flexibility, toughness, and ease of processing, LDPE is an essential material in various industries. This guide will explore the properties, benefits, applications, and processing methods of LDPE, highlighting why it is a preferred choice for many applications.
What is LDPE?
LDPE is a type of polyethylene characterised by its low density (typically 0.910 to 0.940 g/cm³) and high branching. The high degree of branching in its molecular structure prevents the polymer chains from packing closely together, resulting in a less dense and more flexible material. LDPE is produced through the polymerisation of ethylene gas under high pressure and temperature conditions, typically using free-radical polymerisation.
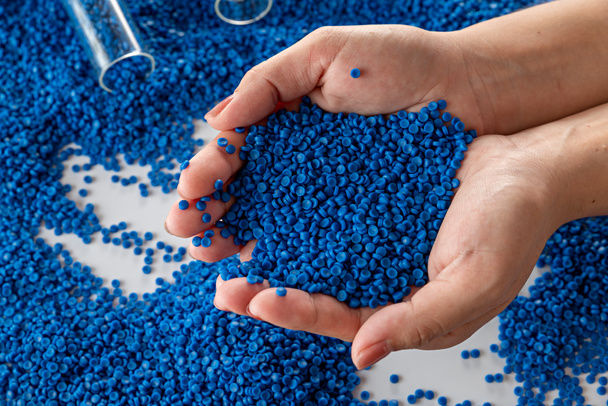
Key Properties of LDPE
Flexibility: LDPE is highly flexible, making it ideal for applications that require bendable materials.
Impact Resistance: It has excellent impact resistance, which contributes to its durability in various uses.
Chemical Resistance: LDPE is resistant to many chemicals, including acids, alcohols, and bases, enhancing its suitability for various industrial applications.
Moisture Barrier: It has low moisture permeability, making it an excellent material for packaging applications.
Transparency: LDPE can be made into clear films, allowing for visibility of the packaged contents.
Ease of Processing: The material is easy to process using various methods, facilitating its use in different forms and applications.
Applications of LDPE
The unique properties of LDPE make it suitable for a wide range of applications, including:
Packaging: Plastic bags, films, and sheets due to its flexibility and moisture barrier properties.
Containers: Bottles and squeezable tubes for products like cosmetics and food.
Agriculture: Greenhouse films and irrigation tubing.
Consumer Goods: Toys, household items, and kitchen utensils.
Electrical Insulation: Coating for wires and cables.
Construction: Protective films and membranes for various building applications.
Medical Products: Disposable gloves and packaging for sterile instruments.
Processing Methods for LDPE
LDPE can be processed using several methods, depending on the desired end product:
Blow Moulding: Used to create hollow objects like bottles and containers by expanding the plastic into a mould using air pressure.
Film Extrusion: Commonly used for producing plastic films and bags by extruding molten LDPE through a die and then stretching it into thin sheets.
Injection Moulding: Used for producing complex shapes and parts, such as lids and closures, with high precision.
Rotational Moulding: Utilised for creating large, hollow products like tanks and containers by heating and rotating a mould filled with LDPE powder.
Thermoforming: Involves heating LDPE sheets and forming them over a mold to produce items like trays and containers.
Advantages of Using LDPE
Versatility: Suitable for a wide range of applications due to its flexible and durable nature.
Ease of Processing: Can be easily shaped into various forms using different processing techniques.
Cost-Effectiveness: Relatively low-cost compared to other polymers, providing a cost-effective solution for many applications.
Chemical and Moisture Resistance: Enhances its use in packaging and industrial applications.
Recyclability: LDPE can be recycled, contributing to environmental sustainability.
Challenges and Considerations
While LDPE offers many benefits, there are some challenges to consider:
Thermal Sensitivity: LDPE has a lower melting point (around 105-115°C) and can deform under high temperatures.
Mechanical Strength: It has lower tensile strength compared to other polyethylene variants like HDPE, limiting its use in load-bearing applications.
Environmental Impact: Although recyclable, LDPE waste can contribute to environmental pollution if not properly managed.
Conclusion
Low-Density Polyethylene (LDPE) is a highly adaptable and widely used material, valued for its flexibility, durability, and ease of processing. Its extensive use in packaging, construction, agriculture, and consumer goods underscores its importance in various industries. By understanding the properties, benefits, and processing methods of LDPE, you can leverage its advantages in your applications, ensuring efficiency and performance. Whether you’re designing flexible packaging solutions, producing durable consumer products, or developing protective films, LDPE offers the versatility and reliability needed to meet your project requirements.
If you're considering plastic injection moulding for your components and want to explore how LDPE can benefit your products, schedule a free consultation with us today. Our team is ready to assist you.
Comments